At Scitek we can cater to your manufacturing needs, ranging from sample preparation for coating processes to metallisation and deposition procedures for the semiconductor, solar, battery, automotive, battery and decorative industry
Thermal Evaporation
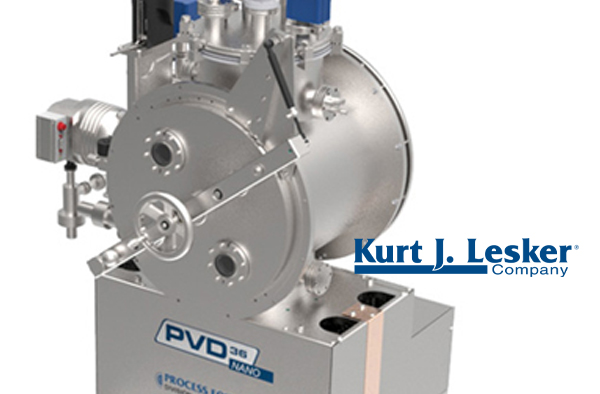
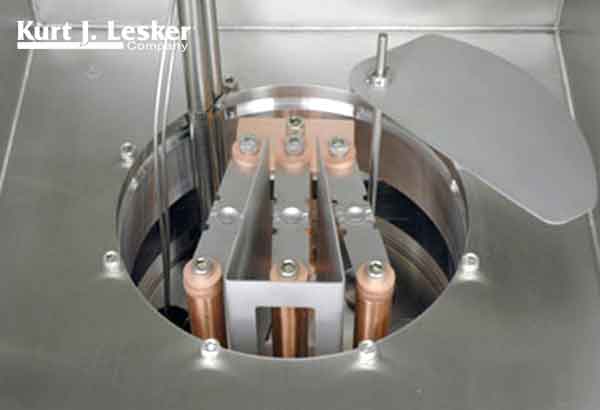
Thermal evaporation is a technique that uses high current through a metal electrical resistance whereby the material to be deposited is placed.
The heat produced causes the material to sublimate in the form a vapour and coats the substrate. This is typically used in the automotive industry in coating head lights or using it to apply metallic finishes (eg gold, silver, chrome) in the decorative and cosmetic industry.
E-Beam Evaporation
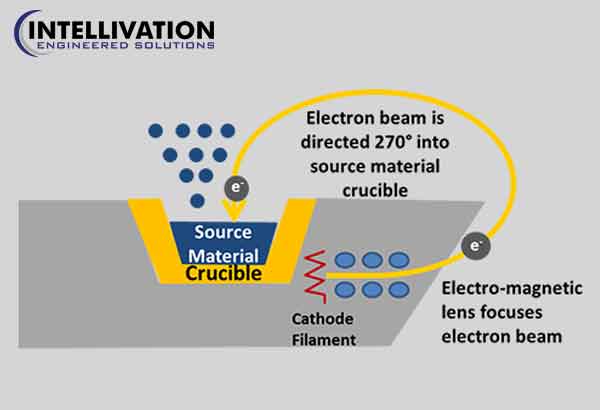
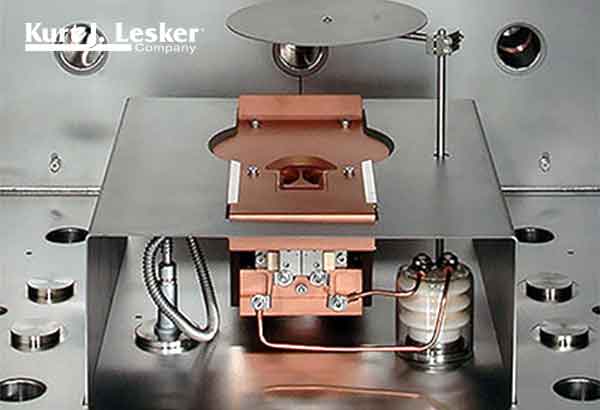
E-beam evaporation is a high-vacuum deposition process where a focused electron beam heats and vaporises a target material, such as metals, alloys, or ceramics. The vaporised material condenses onto a substrate, forming a thin, uniform film with excellent adhesion. This process is ideal for achieving coatings with superior precision and performance in challenging industrial environments.
Sputtering
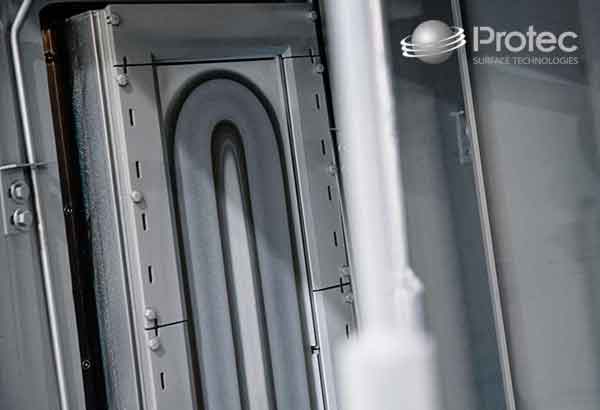
Sputtering is a vacuum-based coating process where a target material is bombarded with high-energy ions, causing atoms to be ejected and deposited onto a substrate. The result is a thin, uniform coating with exceptional properties like hardness, wear resistance, and corrosion protection. The evaporated metal can also recombine with a process gas to create a thin film deposit on products, this is known as reactive sputtering.
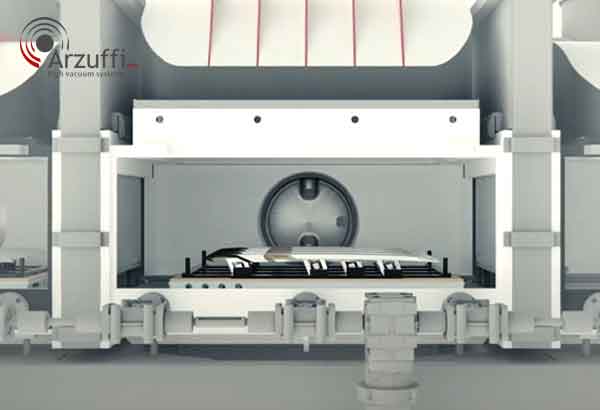
Protec Surface Technologies offer different sputtering configurations which are:
- Balanced Magnetron Sputtering
- Unbalanced Magnetron Sputtering (UBM)
- Dual Magnetron Sputtering
- RF Magnetron Sputtering
- HiPIMS
These configurations are designed to offer different features whether it be for surface hardness, corrosion resistance or resistance to UV light.
Physical Vapour Deposition (PVD)
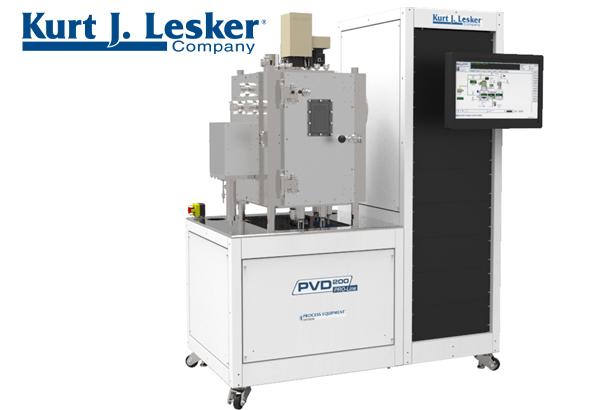
Physical Vapour Deposition, or PVD, involved the physical transfer of material from a source to a substrate – typically vapourisation of a solid, or liquid source material, which then condenses onto a substrate to form a thin film. Kurt J Lesker provide the material science market with highly versatile and broadly applicable range of Physical Vapour Deposition (PVD) Thin Film Solutions, also encompassing Chemical Vapour Deposition (CVD) and Atomic Layer Deposition (ALD). With hundreds of systems in use worldwide, they will accommodate many configurations with either glovebox integration, load lock; and further more can combine multiple techniques like e-beam, low-temperature evaporation (LTE) sources, thermal evaporation and magnetron sputtering sources. Systems are in use in applications from wear-resistance to data storage, decorative coatings to optics and display technologies, superconductors to semi-conductors, and fundamental physics research, in for example nanotechnology and spintronics that leverages the quantum mechanical property of electron spin to enhance functionality and performance.
Cathodic Arc Evaporation (CAE)
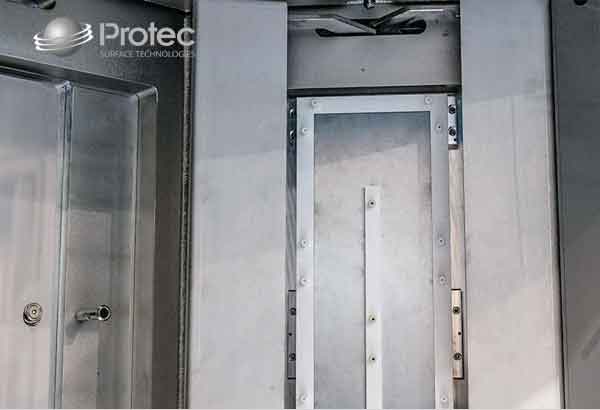
Cathodic Arc Evaporation is a PVD coating process in which a high-energy arc discharge is used to vaporize a target material, creating a plasma that deposits a thin film onto a substrate. This technique results in dense, hard coatings with excellent adhesion, wear resistance, and a high degree of ionization, ensuring superior quality and performance in a wide range of applications.
The ionised evaporated metal combines with a process gas to create a thin film deposit on products rotating in the vacuum chamber.
Materials such as titanium nitride (TiN) or zirconium nitride (ZrN) are used in the decorative industry to provide the aesthetic appeal whilst ensuring scratch and wear resistance.
Plasma-Enhanced Chemical Vapor Deposition (PECVD)
PECVD is a process in which the coating material known as precursor gases or vapours are introduced into a vacuum chamber and activated using plasma. The energized plasma breaks down the gases, allowing the reactive species to bond and form a thin film on the substrate surface.
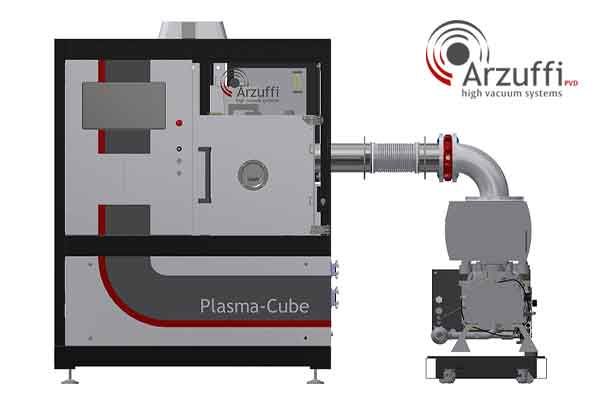
A type of PECVD is DLC (Diamond Like Carbon) coatings, which have Sp3 (diamond-like) and Sp2 (graphite-like) carbon bonds.
It is an innovative coating that is used to enhance friction coefficient or improve hardness of a certain material.
PECVD’s distinguishing features are mainly the process developed at medium-low temperature and low energy and gas/raw material consumption.
Roll-to-Roll PVD Technology

Roll-to-Roll PVD is a vacuum-based coating process designed for the continuous deposition of thin films onto flexible substrates, such as plastic, metal foils, or textiles. Unlike batch processes, R2R PVD allows for large-scale, high-speed coating, making it an efficient and cost-effective solution for industries that require consistent and high-quality coatings over extensive surface areas.
Intellivation R2R vacuum web coating systems can be configured to have different evaporation processing zones such as planar sputtering magnetrons, rotary sputter magnetrons and thermal or e-beam evaporation. They can also incorporate plasma surface treatment zones sich as glow discharge and anode layer ion source.
Slot-die Coating
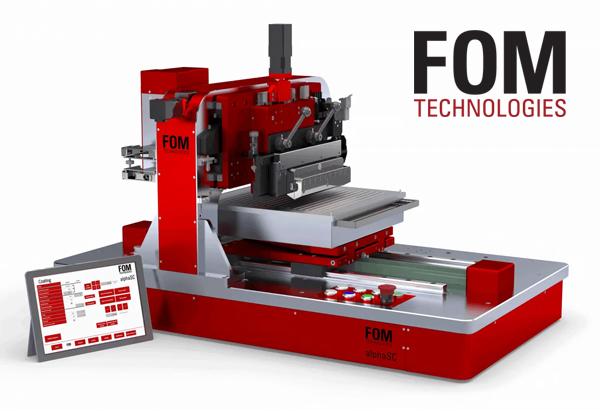
Slot-die coating is a highly scalable technique for rapidly depositing thin and uniform films with minimal material waste and low operational cost. FOM offer sheet based, roll based and roll-to-roll based machines that can deposit uniform dry films from nanometers to microns in thickness. Slot-die coating technology is usable to coat materials such as glass, metal, and polymers. This is achieved by precisely metering the process fluid; dispensing it at a controlled rate while the coating die is moved relative to the substrate. FOM Technologies specialise in machines and equipment for slot-die coating of functional materials. Application areas include but are not limited to development of advanced battery chemistries and architectures, development of next generation PV technologies via roll-to-roll and sheet-to-sheet techniques, and Power-to-X.
Plasma
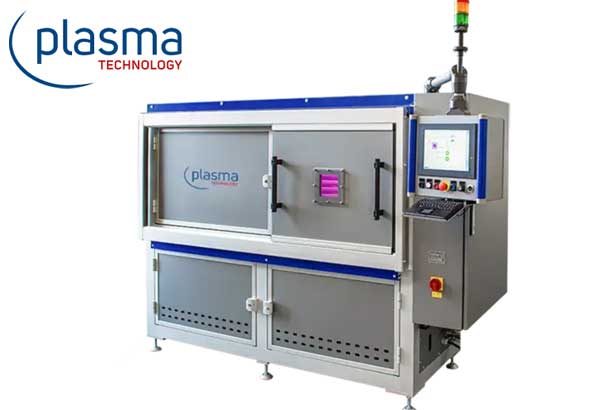
Plasma Technology specialise in a full line of plasma process technology from lab RnD to pilot and production scale.
Our production plasma systems are versatile and can be programmed to carry out multiple tasks, from cleaning to bond and paint adhesion improvement, surface modification and activation or sterilisation, and more.
Most of the mechanical design variations are to ensure optimal product handling or integration into production lines. Depending on the item to be processed, almost any design can be realised from roll-to-roll, drum systems or large surface area and standard bulk batch tray processing. Generally and customization is focused on product handling and automation. Processing products with different geometries, improved integration into production featuring separation of treated product from raw product.
Potential Free Atmospheric Plasma
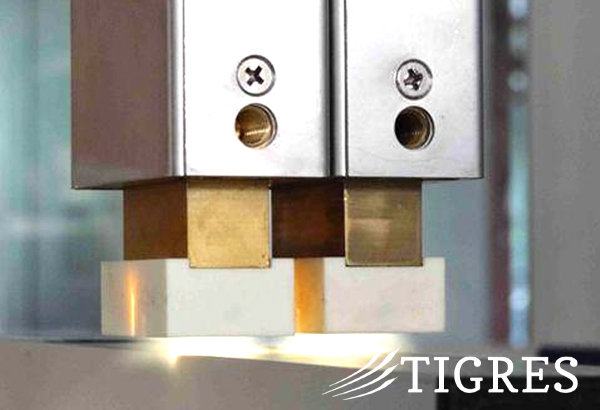
Atmospheric plasma is commonly used in industrial and manufacturing settings for surface treatment, surface cleaning and surface activation – often as preparation step for bonding or coating applications. Different types of atmospheric plasma have varying effects based on electrode types, electrode materials, plasma frequency, gas, plasma temperatures and much more. Our solutions range from small experimental systems for research to large area solutions that can be integrated into industrial automation and robotics.
Leak Detection
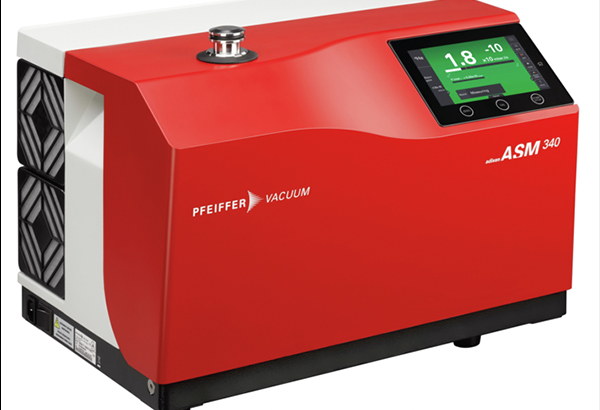
Tracer gas leak detection is a method used to locate leaks in various systems by introducing a tracer gas, like helium or hydrogen, into the system. Pfeiffer Vacuum offers advanced solutions for tracer gas leak detection. They offer a comprehensive suite of leak solutions encompassing various detection methods. Pfeiffer Vacuum’s solutions ensure product integrity, safety, and environmental compliance, making them vital across industries.
Industrial Vacuum
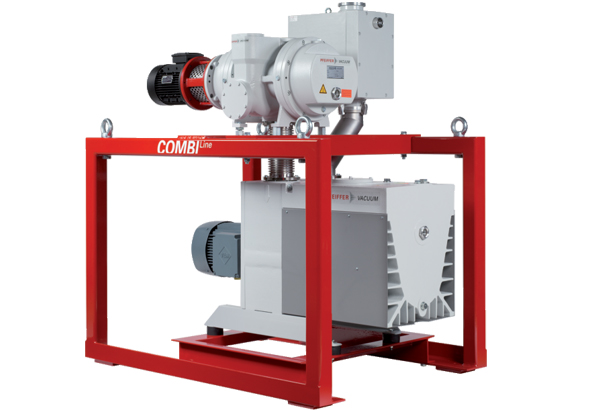
Scitek offers a wide range of solutions for industrial vacuum needs. This includes CombiLine pumping stations for rough vacuum requirements as well as heavy duty high vacuum systems including our turbo and cryo pumps. Our system are tailored to your specific application needs. We customise by selection of appropriate pumping technology and add valving, gauges and control systems to suit.
Deposition Materials
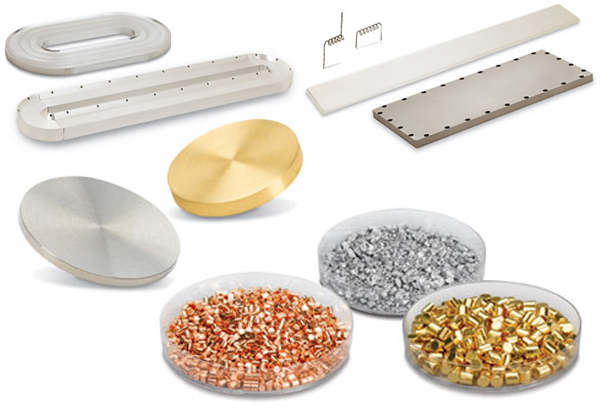
Scitek offers a wide range of industrial materials for PVD. This includes battery materials, materials for catalysis, fuel cells, electro-optics just as much as it includes material for functional and decorative coatings. We also offer material reclaim services for existing customers.